Connect With
Accelera

Want a Quotation or a Demo of our Services?
Don't want to wait?
Picking Perfection: Evaluating Warehouse Techniques for Effective Order Fulfillment
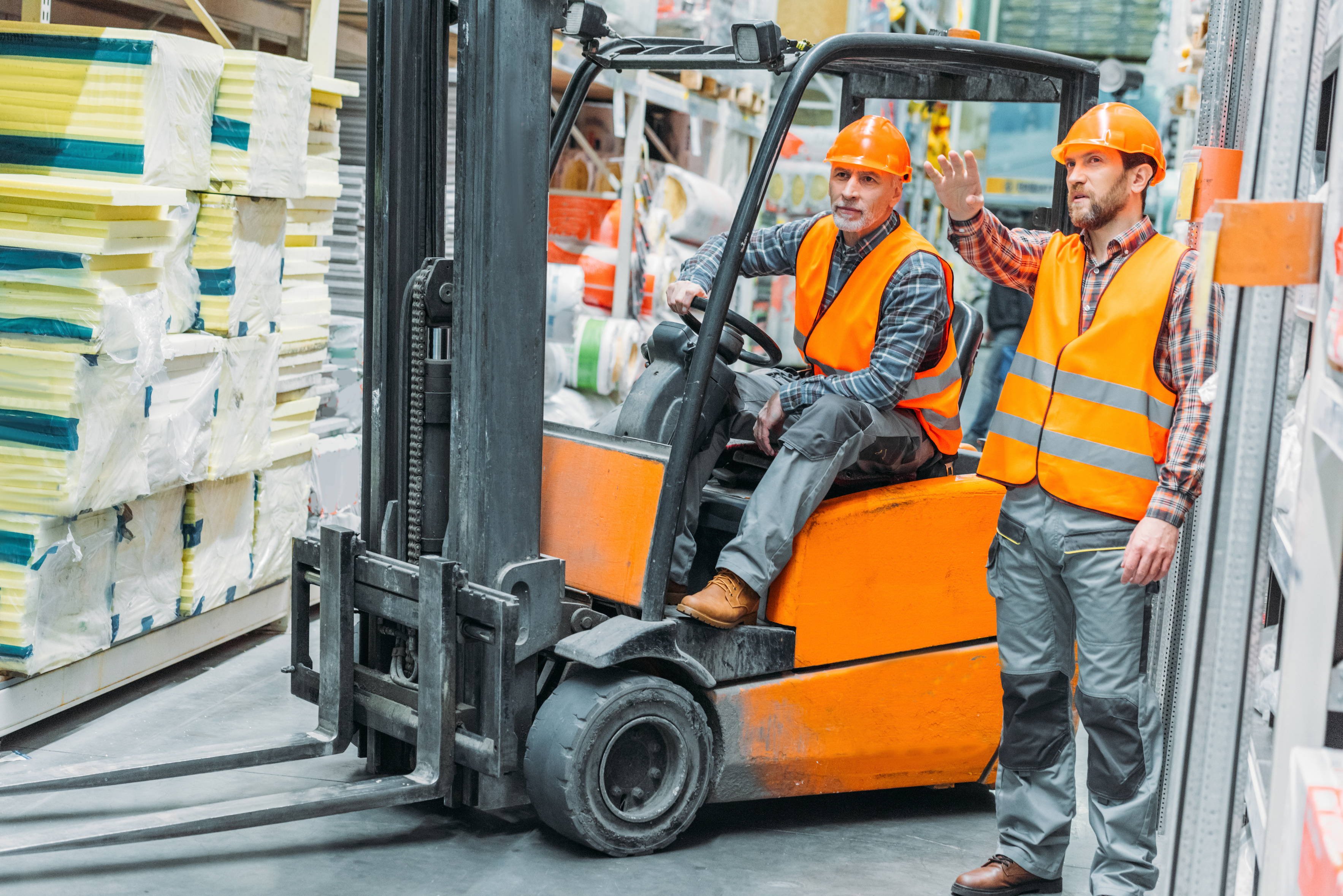
Optimizing Warehouse Picking Methods for B2B Efficiency
Efficient order picking is vital for B2B companies looking to deliver exceptional customer service through accurate and timely order fulfillment. However, with various picking methods available, determining the optimal approach can be challenging based on your inventory profile, facility size, and order characteristics.
In this article, we'll explore common picking methods employed in B2B warehouses and key factors to consider when selecting your approach.
Discrete Order Picking: Flexibility for Low-Volume Orders
Discrete order picking involves processing orders individually from start to finish before moving to the next order. Workers pick products from their respective storage locations to assemble specific customer orders. This method provides flexibility for B2B warehouses handling low order volumes or large, bulky items.
Batch Picking: Efficiency for High Order Volumes
For B2B facilities processing many small orders with common items, batch picking maximizes efficiency. Orders get grouped into batches, and pickers collect items for multiple orders in one pass through the warehouse. The picked items then get sorted into individual orders.
Zone Picking: Optimized Operations in Larger Warehouses
In zone picking, the warehouse gets divided into zones, with assigned pickers responsible for only picking items from their area. This minimizes travel distance in large B2B warehouses. Completed orders get consolidated post-picking. Zone picking works best when order volumes are balanced across zones.
Wave Picking: Grouping Orders with Shared Attributes
Wave picking combines batch picking with zone picking by grouping orders into batches or “waves” based on shared criteria like delivery date or product type. Pickers collect items for each wave’s orders from their assigned zone. This approach reduces travel time and optimizes order grouping.
Pick-to-Cart or Pick-to-Light: Expediting Fulfillment
B2B warehouses can further optimize picking by using carts or pick-to-light systems. Carts get pre-loaded with instructions to follow a predetermined path. Lights signal item locations to minimize errors and movement. Both methods speed up picking for high-volume environments.
Given the many factors at play, leading B2B companies use a combination of these methods to meet their specific warehouse needs. At Accelera, our experienced team can assess your operations and recommend solutions to optimize picking productivity. Our Smart Flow WMS also seamlessly adapts to orchestrate the ideal picking methods and inventory routes based on data and constraints.
Ready to discuss how to reduce logistics costs and scale your B2B order fulfillment? Reach out today to see how Accelera can help.
The Future is Now
Harness the power of intelligent logistics with Accelera. Navigate the complexities of today's fast-paced business environment and stay ahead of the curve as we empower you to excel in a competitive landscape.