Connect With
Accelera

Want a Quotation or a Demo of our Services?
Don't want to wait?
Cutting Out the Clutter: Some Down-to-Earth Tips to Tackling Redundancies in B2B Logistics
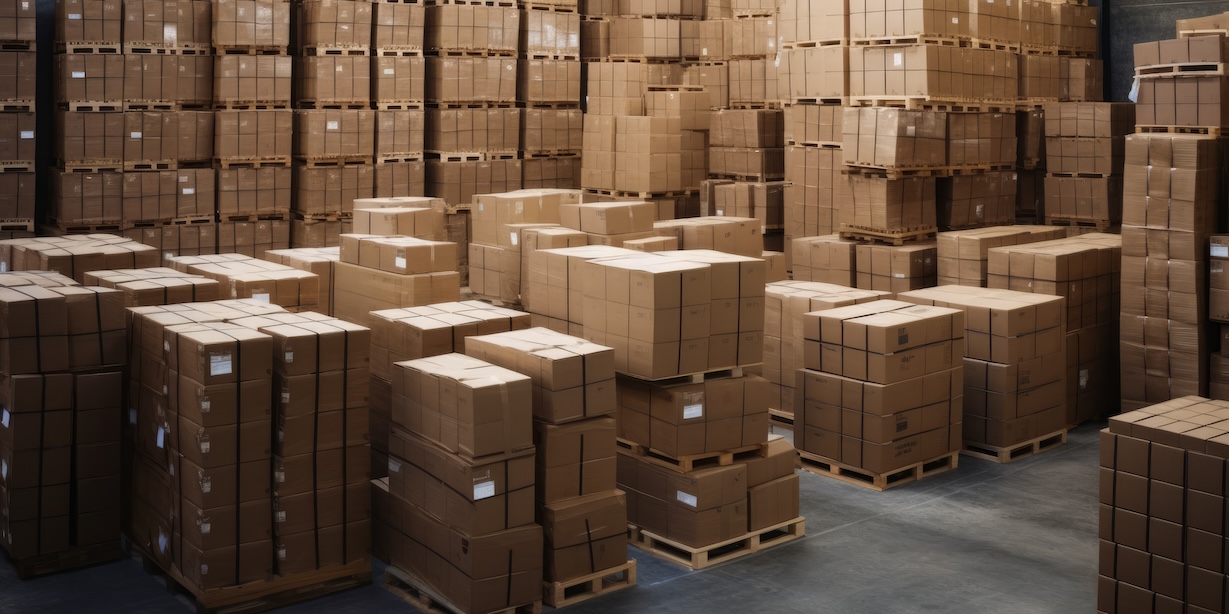
Redundancies in B2B logistics are like the unwanted guests at a party, hogging resources, causing confusion, and quite frankly, overstaying their welcome. Here's a look at why it's worth giving these party crashers the boot.
Understanding Redundancies
Redundancies come in all shapes and sizes. From the painstakingly repetitive task of entering the same data into different systems (we've all been there, right?) to the overstocked inventory that's sitting in your warehouse like a forgotten relic. These are the hiccups that can slow down your logistics groove.
The Impact of Redundancies
When redundancies stick around, they're not just annoying - they're expensive. Imagine pouring time, money, and energy into processes that don't need to be there in the first place. Not the best use of resources, right? Plus, they can slow things down, making it harder to meet client demands on time. And let's not forget about client satisfaction - that's a biggie.
Strategies for Identifying Redundancies
Now, onto the how. Identifying redundancies might seem like finding a needle in a haystack, but with process mapping and data analysis, it's more like a game of 'Where's Waldo?' By drawing out your processes, you can spot the bottlenecks and the activities that are just adding noise, not value. Need some help getting started with process mapping? Check out our post, Process Mapping and Data Analysis: Two Strategies to Reduce Redundancies.
Tips for Eliminating Redundancies
So, how do we give redundancies the old heave-ho? Here are a few strategies:
1. Process Automation: Let's face it, we're in the 21st century, and there's a tech solution for nearly everything. Why waste time doing manual tasks that a computer can do faster and with fewer errors?
2. Lean Principles: Ever heard of Just-In-Time (JIT)? It's a nifty concept that helps you keep just enough inventory to meet demand, reducing the costs and space tied up in excess stock.
3. Continuous Improvement: This one's about keeping things fresh and up-to-date. Regularly tweak and adjust your processes to stay efficient and responsive to changing business needs.
Alright, there you have it - your quick tips to showing redundancies the door. By spotting and eliminating them, you can streamline operations, boost efficiency, and save a pretty penny.
If you're ready to take your logistics operations from cluttered to streamlined, Accelera has your back. We specialize in creating tailored strategies that address your unique challenges and help you hit your business goals out of the park. Ready to get started? Contact us today and let's get started building your success story together!
The Future is Now
Harness the power of intelligent logistics with Accelera. Navigate the complexities of today's fast-paced business environment and stay ahead of the curve as we empower you to excel in a competitive landscape.