Connect With
Accelera

Want a Quotation or a Demo of our Services?
Don't want to wait?
Batch Picking: The Superpower That Drives Warehouse Efficiency
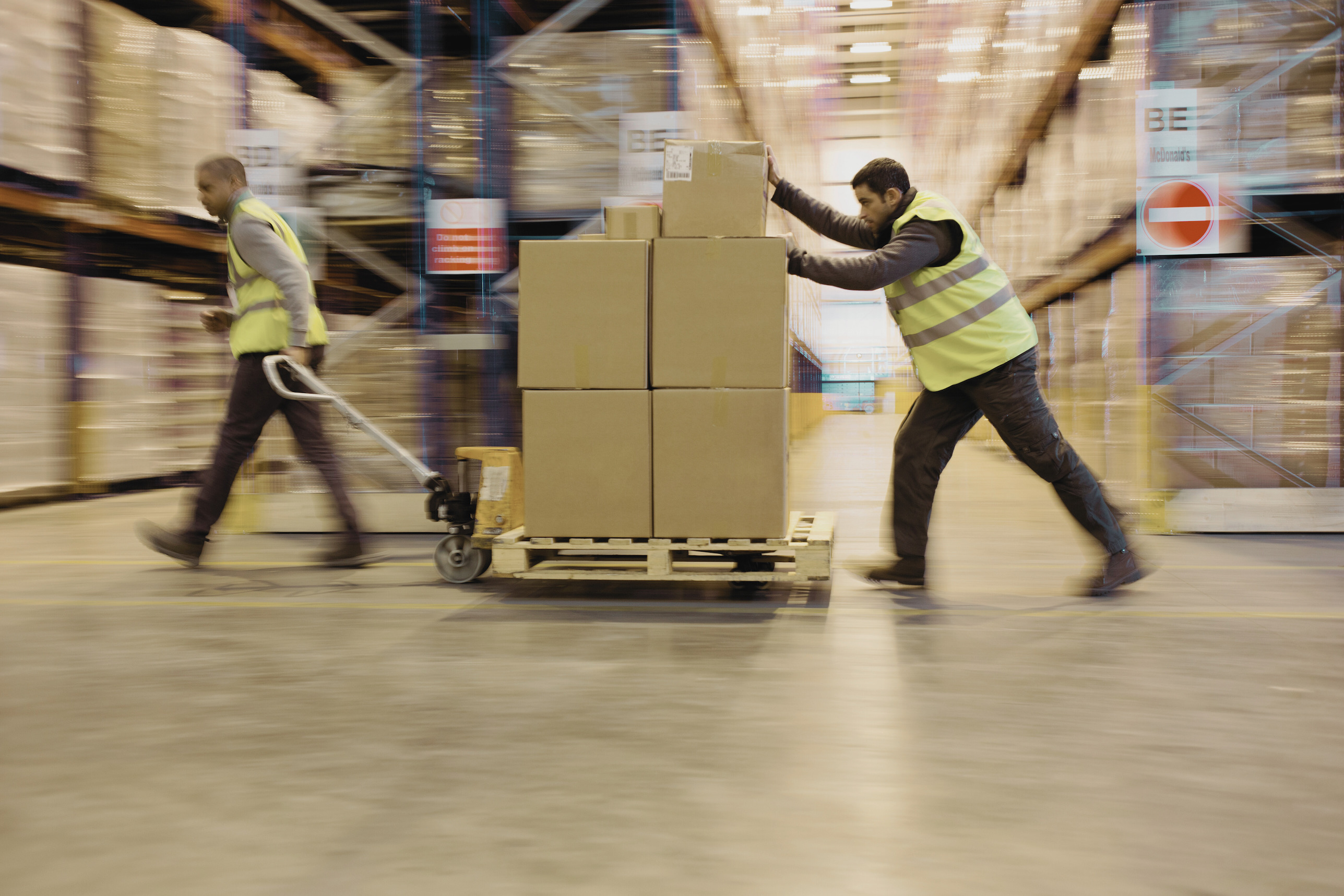
For B2B companies with high order volumes, implementing batch picking in the warehouse can significantly increase fulfillment efficiency and reduce labor costs. But how do you optimize batch picking to maximize its advantages? This brief but in-depth guide covers key batch picking considerations.
What is Batch Picking?
Batch picking, also known as batch order picking, involves grouping orders with similar characteristics to be picked in batches by warehouse personnel. Instead of picking orders one by one, pickers can collect all the items for multiple orders in one trip through the warehouse.
After batch picking is complete, the picked items are sorted and consolidated back into individual customer orders. This approach reduces travel time within the warehouse compared to discrete order picking.
Key Benefits of Batch Picking
Increased picking productivity - By picking for multiple orders simultaneously, workers make far fewer trips, increasing lines picked per hour.
Lower labor costs - Higher picker productivity translates into lower labor costs per order. Batch picking lets you do more with fewer pickers.
Improved capacity - Batch picking increases warehouse throughput and order processing capacity through higher productivity.
Optimized picker travel - Grouping orders into batches minimizes traverse through the warehouse to reduce unproductive travel.
Scalability - As order volumes grow, batch picking allows easy scalability by improving efficiency.
Factors to Optimize Batch Picking
Batch Size: The number of orders in each batch impacts efficiency. Too few orders leads to excessive trips. But extremely large batches can overwhelm pickers. Analyze order size distribution and aim for between 10-30 orders per batch for optimal results.
Order Grouping: Use algorithms to group orders with more shared/closer SKUs into batches. Avoid combining orders with only a few common items. Prioritize grouping orders with high item overlap.
Storage Layout: Position fastest moving items near the middle aisles of storage zones. Store slower movers on the outer edges. This lets pickers efficiently grab more popular items for each batch.
Replenishment Frequency: Replenish pick faces more often for fastest movers to prevent stockouts. Use pick-to-light systems to alert replenishment needs. Prioritize real-time inventory visibility.
Picker Specialization: Consider zone picking where pickers specialize in certain products/areas to improve familiarity. Or have pickers rotate across zones to equalize workloads.
Picking Routing: Use routing algorithms in your WMS to plan optimal pick paths and assign batches intelligently based on constraints like aisle congestion.
Clearly, batch picking requires analysis of multiple factors from batch sizes, to storage placement, to order grouping criteria. At Accelera, our logistics experts can help assess your operations and product profile to determine ideal batch picking parameters. Our Smart Flow warehouse management software also dynamically adapts batch building and picker routing based on real-time data and constraints. The result? Maximum productivity and cost savings.
Want to learn more about leveraging batch picking to improve your B2B fulfillment performance? Contact our team today.
The Future is Now
Harness the power of intelligent logistics with Accelera. Navigate the complexities of today's fast-paced business environment and stay ahead of the curve as we empower you to excel in a competitive landscape.